Effective Cleaning and Servicing of Oil Interceptor Systems
Introduction
Oil interceptors, also known as oil-water separators, are essential in various industries to prevent oil and debris from entering the drainage systems and causing environmental pollution. Thorough maintenance and cleaning are crucial for effective functioning. This case study explores the process of cleaning and servicing oil interceptors to address the challenge of debris removal from oily water.
Problem/Challenge
A medium-sized manufacturing facility faced significant challenges with its oil interceptor system. Over time, debris such as dirt, leaves, and other solid materials accumulated in the oil interceptor, reducing its efficiency in separating oil from water. This resulted in several issues, three of which included:
- Reduced Efficiency: The system was no longer effectively separating oil from water, leading to potential environmental contamination.
- Regulatory Non-Compliance: The facility risked failing to meet environmental regulations and standards.
- Operational Downtime: Frequent blockages and reduced capacity caused interruptions in the facility’s operations.
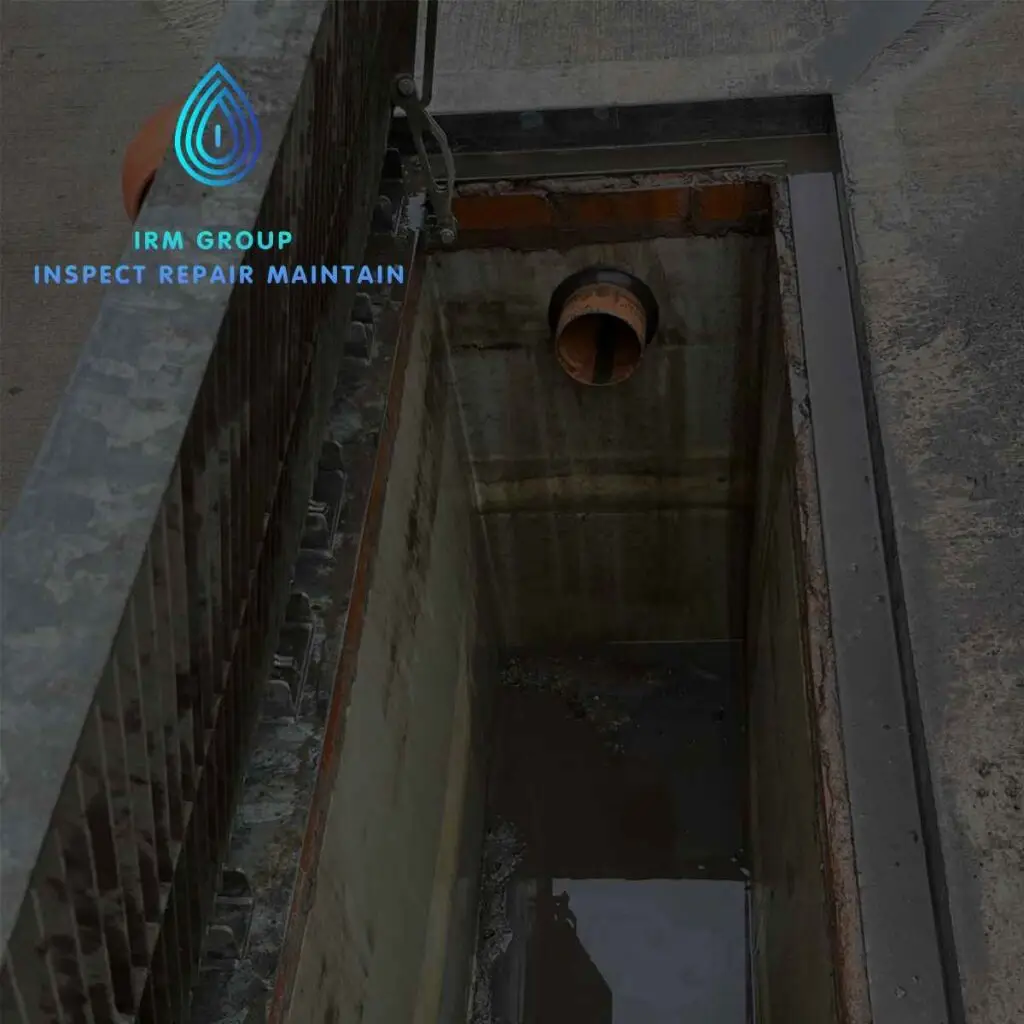
Solution
The facility engaged with IRM Group to address the issue. The company implemented a multi-step approach to clean and service the oil interceptor system effectively.
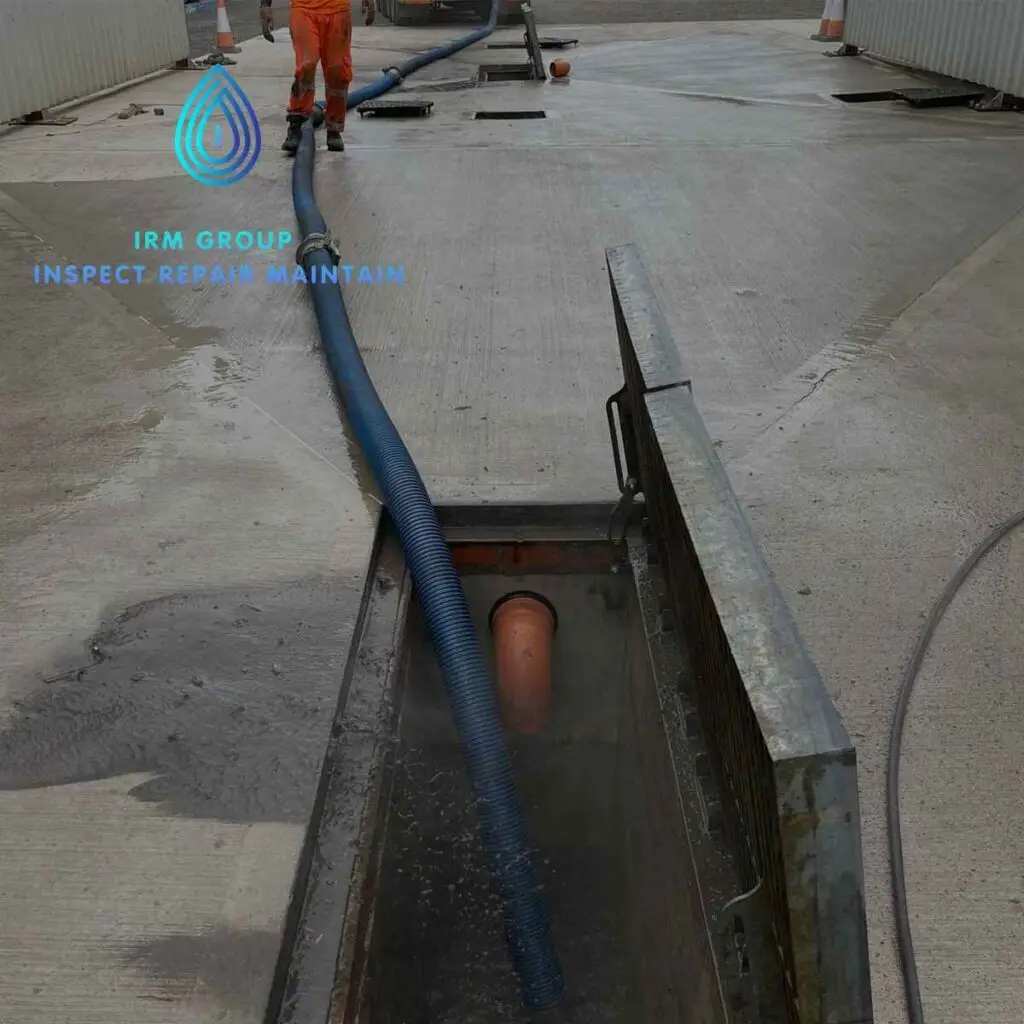
Initial Assessment and Planning
- Conducted a thorough inspection of the oil interceptor system to assess the extent of debris accumulation and oil contamination.
- Developed a detailed cleaning plan, including safety protocols and environmental protection measures.
Debris Removal
- Employed high-powered jet vac recycler to remove accumulated debris and sludge from the interceptor.
- Used specialised high pressure water to dislodge stubborn deposits from the interceptor walls and base.
System Inspection and Maintenance
- Conducted a comprehensive inspection of the cleaned interceptor system to identify any structural issues.
Regular Maintenance Schedule
- Developed a regular maintenance schedule for the facility to prevent future debris accumulation and ensure continuous efficient operation of the oil interceptor system.
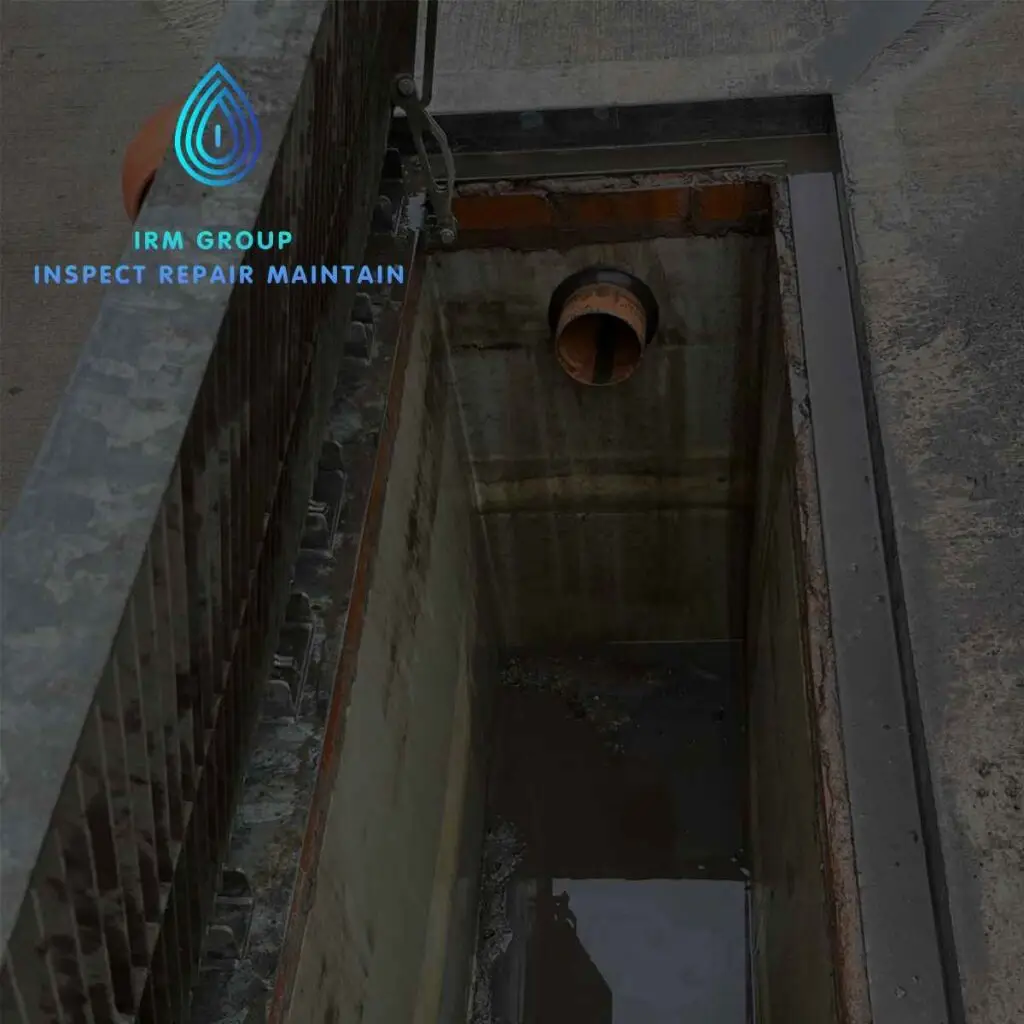
Outcomes
The cleaning and servicing of the oil interceptor system yielded significant positive outcomes for the manufacturing facility:
– Restored Efficiency: The oil interceptor system regained its optimal efficiency, effectively separating oil from water and preventing environmental contamination.
-Regulatory Compliance: The facility met all relevant environmental regulations and standards, avoiding potential fines and legal issues.
– Cost Savings: Preventative maintenance reduced the need for emergency interventions and costly repairs, resulting in overall cost savings for the facility.
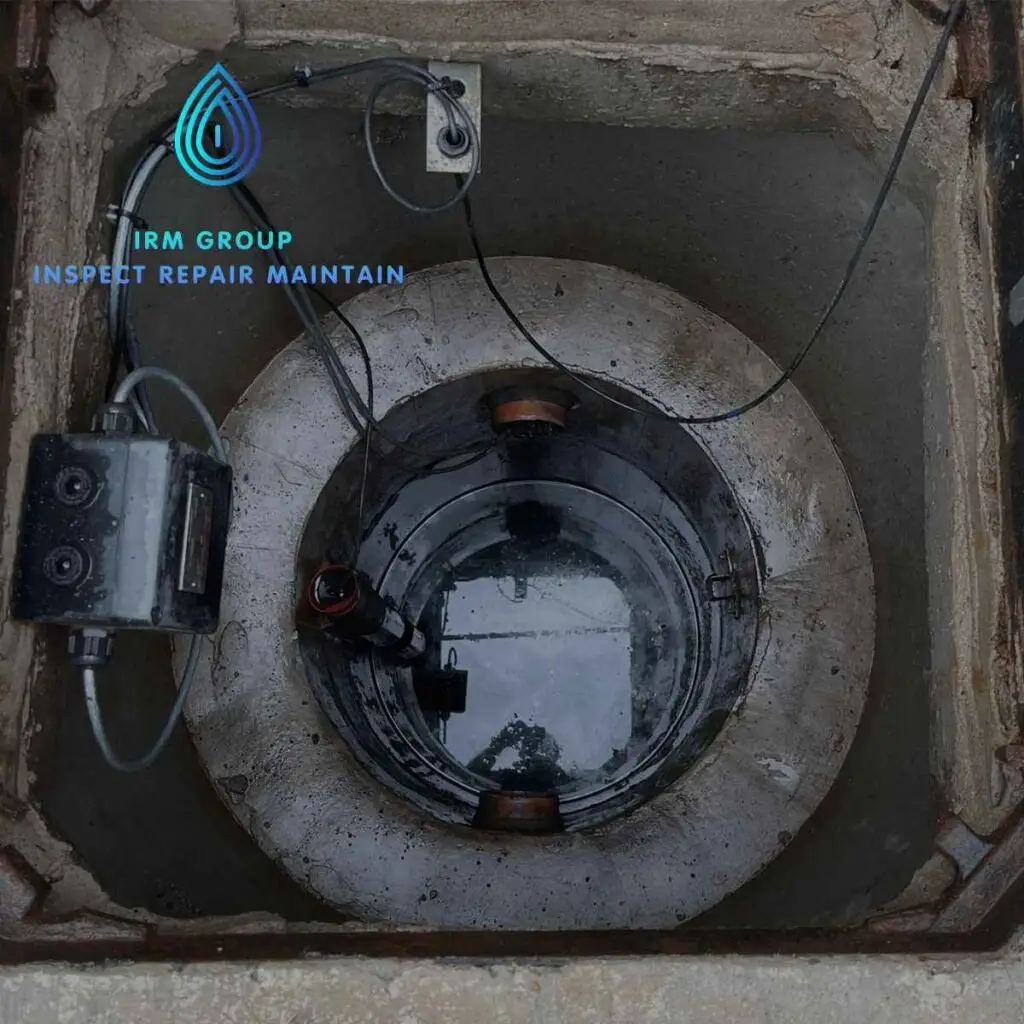